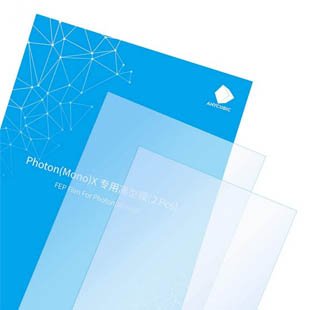
در فرایند پلیمر نورپز از مایعات ، رزین هایی خشک شونده تابشی و یا پلیمر نورپز به عنوان مواد اولیه مورد استفاده قرار می گیرند.بیشتر پلیمرهای نورپز به تشعشاتی با طول موج های ماورای بنفش (UV) واکنش نشان می دهند، اما بعضی از سیستم های نوری قابل رویت نیز در این کا استفاده می شوند. در زمان تابش ، این مواد دست خوش واکنش های شیمیایی می شوند تا اینکه سخت تر گردند. این واکنش را بسپارش نورپز می نامند که به صورت معمول ترکیبی از چندین عنصر شیمیایی می باشد.
توسعه پلیمر های نورپز در اواخر سال 1960 شکل گرفت و به سرعت در چندین زمینه تجاری به کار گرفته شدند، که صنایع رو کش و چاپ از بارزترین آنها می باشد. برای مثال بسیاری از پوشش های براق روی کاغذ یا کارتن ها از پلیمر نورپز ساخته شده اند. علاوه بر این، رزین های خشک شونده نوری در دندانسازی در مواردی مانند روکش بالای دندان جهت پرکردن شیارها و جلوگیری از وجود حفره درون آنها، استفاده می شود. در این کاربردها، روکش ها با استفاده از تشعشات خشک می شوند و با این کار رزین ها بدون احتیاج به الگودهی مواد یا تشعشات سطوح را می پوشانند. این کار با ارائه لیتوگرافی سه بعدی، اولین فرایند بسپارش نورپز مخزنی، تغییر می کرد. همچنین با مراجعه به فروشگاه آذرین 3D میتوانید از خریدن پرینتر سه بعدی بهره کافی ببرید.
مقدمه
در اواسط 1980، چارلز(چاک) هال، همانند سیستم های موجود در چاپ لیزری، با قرار دادن مواد خشک شونده UV درمعرض اسکن لیزری مورد آزمایش قرار داد. او متوجه شد که الگوهای پلیمری یکپارچه قابل تولید هستند. او توانست با خشک کردن یک لایه بر روی لایه قبلی، یک قطعه سه بعدی یکپارچه تولید کند و این کار تازه شروع فعالیت تکنولوژی لیتوگرافی سه بعدی (SL) بود. اندکی بعد از آن شرکت 3D System ایجاد شد و دستگاه های SL را به عنوان دستگاه - های « نمونه سازی سریع » در صنایع توسعه محصول، تجاری سازی کرد. از آن زمان به بعد، انواع مختلفی از فرایندها و تکنولوژی های مربوط به SL گسترش یافت. واژه « بسپارش نورپز مخزنی » یک اصطلاح کلی است که SL و فرایندهای مربوطه را در برمی گیرد. SL به شکلی خاص در مقیاس ماکرو، در بسپارش نورپز مخزنی اسکن لیزری کاربرد دارد : در غیر این صورت واژه بسپارش مخزنی به صورت VP مخفف شده و به کار برده خواهد شد.
جهت خشک کردن پلیمرهای نورپز تجاری امکان بهره بردن از انواع مختلفی از تشعشات همچون اشعه گاما، اشعه X، پرنوهای الکترون، UV و در بعضی موارد نور مرئی استفاده شود. در سیستم های VP، استفاده از تشعشات UV و نور مرئی بیشتر رواج دارد. در صنایع میکرو الکترونیک، مواد ماسک نوری ( فتومسک) اغلب پلیمر نورپز هستند و معمولا اشعه به صورت UV راه دور و پرتو الکترونی، به آنها تابانده می شود. در عوض، در زمینه دندانپزشکی اغلب از نور مرئی استفاده می گردد.
دو ترکیب جهت توسعه فرایندهای بسپارش نورپز مخزنی، همراه بایک ترکیب اضافی که در بعضی از تحقیقات مورد توجه قرار گرفته است. گرچه پلیمرهای نورپز در بعضی از فرایندهای پرینت جوهرافشان نیز استفاده می شدند. ترکیبات مورد بحث قرار گرفته در این بخش شامل :
• اسکن برداری،یا نقطه ای، که رویکرد های رایج در دستگاه های SL تجاری هستند.
• ماسک پروجکشن یا خطی که در این رویکرد، تابش بر کل لایه های به صورت یکجا انجام می شود.
• رویکردهای دو فتونی که مشخصا شیوه هایی با وضوح بالای نقطه به نقطه هستند.
توجه به این امر که در شیوه های اسکن برداری و دو فتون، نیازمند پرتو های لیزر اسکن می باشد، به طوریکه شیوه ماسک پروجکشن از پرتو تشعشعی عظیمی استفاده می نماید که با یک دستگاه دیگر که در این حالت می تواند ریز آینه دیجیتالی باشد، الگوسازی می شود.در مورد شیوه دو فتونی، بسپارش نورپز در محل تقاطع دو پرتو اسکن لیزری اتفاق می افتد، در حالیکه ترکیبات دیگر، از یک لیزر و ترکیبات آغازگر نوری متفاوتی استفاده می کنند. تفاوت دیگر بین آنها، نیاز به روکش مجدد یا به کارگیری یک لایه جدید از رزین در روش های اسکن برداری و ماسک پروجکشن است، در حالیکه در شیوه دو فتونی، قطعه در زیر سطح رزینی ساخته می شود که دیگر لزومی به ساخت پوشش مجدد نیست. شیوه هایی که نیازی به پوشش مجدد ندارد، سریعتر بوده و پیچیدگی کمتری دارند.
مواد بسپارش نورپز مخزنی
بخشی از پیشینه های پلیمر نورپز UV که برای تمام ترکیبات فرایندهای بسپارش نورپز رواج دارد، موضوع مورد بحث در این بخش می باشد.این قسمت دارای دو زیر مجموعه در مورد میزان واکنش ها و روش های خاص نیز هست.
پلیمرهای نورپز خشک شونده UV
پلیمرهای نورپز در سال های پایانی 1960 توسعه یافتند. علاوه بر کاربردهای دیگرشان، آنها در مقاومت های نوری در صنایع میکروالکترونیک نیز کارآیی دارند. این کارآیی بر توسعه و رشد پلیمرهای نورپز با پایه اپوکسی بیشترین تاثیر را داشته است. مقاومت های نوری در اصل SL های یک لایه هستند که در آن دقت و وضوح زیاد از ویژگی ها الزامی می باشند.
برای خشک کردن پلیمر های نورپز تجاری امکان دارد از انواع مختلف تشعشات استفاده شود که شامل اشعه های گاما،اشعه X،پرتوهای الکترون، UV و بعضی موارد نور مرئی می باشد. گرچه در این میان UV و پرتوهای الکترون رایج ترین آها هستند. در AM بسیاری از این منابع اشعه در تحقیقات مورد استفاده قرار می گیرند، ولی فقط سیستم - های UV و نور مرئی در سیستم های تجاری استفاده می شوند. برای مثال در سیستم -های SL، با وجود اینکه انواع دیگری از تشعشعات قابل استفاده هستند ولی فقط تشعشع قابل استفاده هستند ولی فقط تشعشع UV به شکل وسیعی کاربرد دارد. در SLA-250 از شرکت 3D System، لیزر هلیوم –کادمیوم (HeCd) با طول موج 325 nm مورد استفاده قرار می گیرد. در مقابل، در مدل های دیگر SL، لیزری که برای شرایط منسجم کننده مورد استفاده قرار می گیرد، Nd-YVO4 است. در سیستم های ماسک پروجکشن بر پایه DMD نیز، تشعشع UV و نور مرئی استفاده می شود.
پلیمرهای گرمانرم (ترموپلاستیک ) که معمولا به صورت قالبگیری های تزریقی هستند، دارای یک ساختار مولکولی خطی یا رشته ای می باشند که به آنها امکان ذوب و سخت - شدن مکرر را می دهد. در عوض، پلیمرهای نورپز VP به صورت به هم پیوسته هستند و ذوب نمی شوند در نتیجه خزش بسیار کمتری از خود نشان داده و به تنش گیری هم پاسخ بسیارکمتری می دهند.
نخستین امتیاز انحصاری در ایالت متحده که رزین های SL را توصیف می کرد در سال های 1989 و 1990 منتشر گردید. رزین هایی که از اکریلات هایی با واکنش پذیری بالا بدست آمده بودند معمولا به خاطر خطاهای ناشی از انقباض و خم شدن، قطعات ضعیفی را می ساختند.در رزین های اکریلاتی در زمانی که تصویر از طریق لیزر منعکس می شد، معمولا فقط تا 46% از آن خشک می شدند. وقتی یک روکش تازه بر روی لایه قبلی قرار می گرفت، بعضی از تشعشعات از این روکش تازه گذر کرده واکنش فتوشیمیایی جدیدی درلایه قبلی که فقط بخشی از آن خشک شده بود، ایجاد می کرد. این لایه بعد از اینکه پوشانده می شود، آمادگی کمتری برای جلوگیری از ورود اکسیژن دارد. پیوند عرضی اضافه شده بر روی این لایه موجب انقباض و در نتیجه فشار بیشتر درون این لایه شده و خمیدگی را بوجود می آورد که حتی در طول فرایند ساخت قطعه یا بعد از آن هم مشاهده می شود.
نخستین امتیاز انحصاری که ترکیب اپوکسی را برای رزین های SL فراهم کرد، در سال 1988 در ژاپن بوجود آمد. رزین های اپوکسی نسبت به رزین های اکریلات، قطعات دقیق – تر، سخت تر و مقاوم تری را می ساختند. درحالیکه بسپارش ترکیبات اکریلات منجربه انقباض 5 تا 20 % می شوند، بسپارش حلقه باز از ترکیبات اپوکسی تنها 1 تا 2 % انقباض را ایجاد می کند. این سطح پایین انقباض موجود در ماهیت مواد اپوکسی باعث چسبندگی عالی آن می گردد و تمایل به استفاده از زیرلایه های قابل انعطاف که در طول زمان خشک شدن، خم می شوند را کم می کند. علاوه براین، اکسیژن محیط، مانع بسپارش رزین های اپوکسی نمی شود و این کار کمی را برای تمرکز آغازگر نوری بوجود می آورد که نسبت به ایجاد اکریلیک، بوی کمتری را به جا می گذارد.
مضرات رزین های اپوکسی شامل سرعت کم نور و شکنندگی قطعات خشک شده می - باشد.جهت سرعت بخشیدن به ایجاد مقاومت در قطعه، اضافه کردن مقداری اکریلات به رزین های اپوکسی الزامی است، در نتیجه آن قطعه در طول فرایند ساخت، انسجام کافی برای جابه جایی بدون ایجاد انحنا را دست می آورد. اکریلیت ها همچنین برای کاهش شکنندگی قطعات اپوکسینیز مفید هستند. یکی دیگر از مضرات رزین های اپوکسی، حساسیت آنها به رطوبت است که مانعی برای پلیمر سازی هستند.
سخن تکمیلی
اکثر رزین های SL که امروزه به صورت تجاری در دسترس می باشند، اپوکسی هایی با محتوای اکریلات هستند. استفاده از هردو نوع مواد با ترکیبات یکسان، جهت ترکیب فواید هردو نوع مواد با ترکیبات یکسان، جهت ترکیب فواید هردو نوع خشک کننده، الزامی می باشند. پیشرفت در دقت ناشی از استفاده از رزین های هیبرید، SL را به طرز چشمگیری تقویت می نماید. در کنار تمام این موارد بهتر است بدانید که با مراجعه به فروشگاه آذرین 3D میتوانید از اسکنر سه بعدی نیز بهره کافی ببرید.
نظرات کاربران